現(xiàn)代半導(dǎo)體制造的目標(biāo)是為便攜式產(chǎn)品開發(fā)具有越來越小和更薄封裝的電子設(shè)備。實(shí)現(xiàn)這一目標(biāo)最重要的步驟之一是通過機(jī)械研磨工藝將加工后的硅晶片從背面減薄至 50μm?以下。為了避免應(yīng)力和亞表面損傷,這對(duì)表面粗糙度要求非常高,在最終研磨步驟中,該粗糙度可能在 1 nm Ra 的范圍內(nèi)。
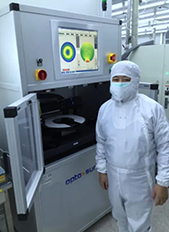
測量這一等級(jí)的表面粗糙度的常用方法是通過共聚焦顯微鏡 (CFM)、白光干涉儀 (WLI) 或原子力顯微鏡 (AFM) 進(jìn)行單點(diǎn)或是劃線測量。但這些儀器的缺點(diǎn)是對(duì)機(jī)械環(huán)境噪聲敏感,測量時(shí)間長。
這里,我們將介紹一種新型的散射光測量方法,該方法能夠在不到 30 秒的時(shí)間內(nèi)測量直徑300 mm整個(gè)晶圓表面。除了粗糙度,傳感器還同時(shí)測量翹曲、波紋度和缺陷。同時(shí)將展現(xiàn)采用不同粒度研磨表面的測試結(jié)果分析。
?
晶圓表面加工工藝過程
極小和高密度電子產(chǎn)品的趨勢需要先進(jìn)的工藝來滿足設(shè)備的厚度和熱性能規(guī)格。這意味著處理后的硅晶片必須從其原始厚度超過 700 μm 減薄至 50 μm 或更小。最常見且成本相對(duì)較低的減薄方法是通過機(jī)械去除殘余硅的背面研磨。晶片固定在多孔真空吸盤上,IC(集成電路)面朝下。砂輪的旋轉(zhuǎn)軸與晶片的旋轉(zhuǎn)軸離軸定位(距離是晶片的半徑)??ūP呈略呈圓錐形的形狀,以很小的傾斜度使晶片變形,以確保砂輪在研磨過程中僅接觸晶片的一半。由于卡盤的旋轉(zhuǎn)和砂輪的同時(shí)旋轉(zhuǎn),在晶片表面上產(chǎn)生了典型的螺旋劃痕圖案。
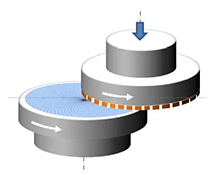
根據(jù)砂輪的粒度以及轉(zhuǎn)速和進(jìn)給率等加工參數(shù),這種機(jī)械沖擊是造成粗糙度、應(yīng)力和誘發(fā)亞表面損傷的原因。因此,現(xiàn)代晶圓磨床從粗砂輪開始,先是快速去除多余硅,最后使用小粒度砂輪進(jìn)行精細(xì)研磨。當(dāng)減薄至 50 μm 以最大程度地減少次表面損傷和應(yīng)力時(shí),這個(gè)最終過程是絕對(duì)必要的。表面粗糙度通常應(yīng)在 Ra<10 nm 甚至 1 nm 的范圍內(nèi),這對(duì)機(jī)械磨床來說是一個(gè)挑戰(zhàn)。晶圓表面的粗糙度是否太高或分布不均勻,后續(xù)的引線鍵合、倒裝芯片組裝、成型和測試等工藝步驟可能會(huì)因破裂而損壞薄芯片。除了低表面粗糙度外,切割后模具的斷裂強(qiáng)度還取決于磨痕的方向。
? 當(dāng)前標(biāo)準(zhǔn)測量方法的局限性是砂輪與其大量單刀刃的相互作用,與硅表面經(jīng)歷不均勻磨損,特別是在應(yīng)用精細(xì)磨削程序時(shí),是一個(gè)相當(dāng)復(fù)雜的過程。因此,不可能通過使用 AFM、WLI 或 CFM 進(jìn)行少量小區(qū)域粗糙度測量來預(yù)測研磨后整個(gè)晶片表面的質(zhì)量。通常,這些標(biāo)準(zhǔn)測量方法中, AFM 的情況下,單次測量的評(píng)估面積在為 20 μm x 20 μm,在 CFM 或 WLI 的情況下為 160 μm x 160 μm。每次測量大約需要 20 s-30 s,并且需要抗振設(shè)備以避免受到環(huán)境機(jī)械噪聲的影響。? ? ?
OptoSurf?WaferMaster 300優(yōu)勢
? ?為了獲得整個(gè)晶圓表面的信息,需要更快、更穩(wěn)健的測量技術(shù)。散射光測量是唯一可以達(dá)到這些要求的方法,Optosurf公司基于散射光測量技術(shù),推出一款新的測量機(jī)器(WaferMaster 300),該系統(tǒng)使用散射光傳感器(如下圖)在不到 30 S的時(shí)間內(nèi)測量整個(gè) 300 mm晶片表面的粗糙度。該系統(tǒng)使用 OS 500 散射光技術(shù),該技術(shù)已在用于超導(dǎo)和醫(yī)療應(yīng)用的高質(zhì)量拋光金屬表面的表面測量中得到充分證明。由于傳感器的特殊設(shè)計(jì),WaferMaster 還可以測量翹曲、波紋度和缺陷。
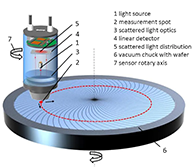
OptoSurf?WaferMaster 300測量原理
WaferMaster WM 300 是一種掃描設(shè)備,其中晶片位于卡盤上,以大約 60 rpm 的速度旋轉(zhuǎn),散射光傳感器垂直放置在表面上方 5 毫米處。每次旋轉(zhuǎn)后,傳感器向晶片中心移動(dòng)一小步。根據(jù)設(shè)置,系統(tǒng)記錄 70,000-700,000 次單次粗糙度測量,大約需要 1-10 分鐘。同時(shí),傳感器測量表面斜率,這是翹曲和波紋度計(jì)算的基礎(chǔ)。
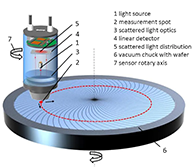
光源 (1) 以 0.9 mm 光斑尺寸 (2) 的 670 nm 紅色?LED 光斑幾乎垂直照射晶片表面。這是具有中等橫向分辨率的快速測量的標(biāo)準(zhǔn)方法。為了獲得高橫向分辨率,可以打開來自具有相同波長的激光源的另一個(gè)直徑為 0.03 mm?的光斑。光學(xué)器件 (3) 收集 32°角度范圍內(nèi)的散射光,并將其引導(dǎo)至線性探測器 (4)。
? 帶有晶片 (6) 的卡盤在測量過程中連續(xù)旋轉(zhuǎn),傳感器從晶片邊緣線性移動(dòng)到中心。隨后,傳感器測量整個(gè)晶圓表面,并在 30 秒內(nèi)以標(biāo)準(zhǔn)方式(0.9 毫米點(diǎn))對(duì) 300 毫米晶圓進(jìn)行約 70.000 次單次粗糙度測量。非常重要的是傳感器的額外旋轉(zhuǎn) (7),因?yàn)榫€性探測器應(yīng)始終垂直于磨痕定向以獲得最大粗糙度值。作為粗糙度參數(shù)Aq,是通過計(jì)算散射光分布的方差得出.φi是單個(gè)散射角,M是重心,p(φ)是分布曲線。
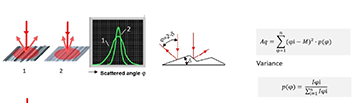
與其他散射光傳感器相比,該傳感器具有第二個(gè)評(píng)估通道,可通過傾斜角分析來測量翹曲和波紋度。該傳感器測量鏡面光(表面的 0°部分)以及由表面微結(jié)構(gòu)產(chǎn)生的散射光。這種設(shè)置的優(yōu)點(diǎn)是能夠使用散射光分布 (5) 的重心作為表面局部幾何變形的信號(hào)。了解表面的局部傾斜角度并以等距離(由編碼器信號(hào)創(chuàng)建)連續(xù)測量表面,可以計(jì)算局部高度,并通過整合所有角度,計(jì)算表面的整個(gè)輪廓。
如下圖所示,測量光束在 2 倍的局部傾斜角?下偏轉(zhuǎn)。因此,散射光分布在線性探測器上偏移了角度值 M??梢酝ㄟ^使用第一個(gè)統(tǒng)計(jì)量來測量散射光分布曲線的矩。知道來自編碼器的步長Δx和光學(xué)元件的焦距,就可以計(jì)算局部高度Δy并通過總結(jié)得出高度輪廓。
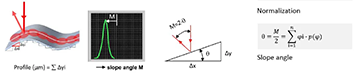
Aq與Rdq、Ra關(guān)系
Aq 的優(yōu)點(diǎn)是與輪廓斜率參數(shù) Rdq 的密切關(guān)系,它很好地描述了表面摩擦。為了遵循將平均粗糙度 Ra 確定為粗糙度值的 Semi 標(biāo)準(zhǔn),通過使用共聚焦顯微鏡對(duì)不同晶片進(jìn)行比較測量,將 Aq 參數(shù)與 Ra 相關(guān)聯(lián)。由于磨削表面振幅分布的隨機(jī)特性,即使在使用不同粒度的砂輪時(shí),Aq 和 Ra 之間也有相當(dāng)好的相關(guān)性。但應(yīng)該考慮到 Aq 是一個(gè)更通用的參數(shù),因?yàn)樗鼘?duì)剖面的垂直和橫向結(jié)構(gòu)都有反應(yīng),而 Ra 只測量平均垂直高度。Aq 的這種特性對(duì)于表征芯片強(qiáng)度可能很有趣,并且應(yīng)該在未來進(jìn)行更詳細(xì)的研究。
相關(guān)性測量 Ra (nm) = f( Aq)
在不同的區(qū)域上研究了幾個(gè)晶片,磨粒尺寸從 #2000 到 #8000。此外,還測量了 Ra 值<1nm 的 CMP 拋光晶片以檢查系統(tǒng)的準(zhǔn)確性。為了計(jì)算 Ra 值,WaferMaster 機(jī)器中使用了擬合的相關(guān)方程。
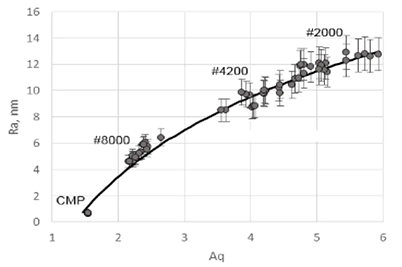
測量結(jié)果展示及分析
傳感器測量散射光粗糙度值 Aq、宏觀傾斜角 M(從中計(jì)算翹曲和波紋度)和強(qiáng)度 I。I 值與從裸晶圓散射光測量系統(tǒng)已知的 TIS 值相關(guān)。在粗糙度圖上,顏色顯示高和低粗糙度區(qū)域。光學(xué)粗糙度值A(chǔ)q是散射光分布曲線的統(tǒng)計(jì)值(方差)?;谂c已知 Ra 值的相關(guān)性,Aq 可以轉(zhuǎn)換為 Ra。只要加工過程不變,這是有效的。翹曲計(jì)算基于撓度法,其中主要值是傾斜角。波紋度由高斯濾波器技術(shù) (ISO 16610) 的翹曲導(dǎo)出。
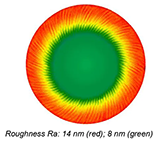
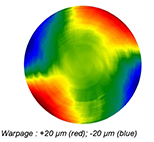
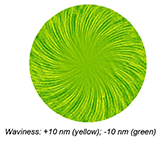
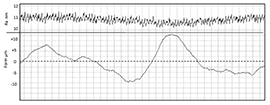
在 300 mm晶圓的 75 mm半徑 (360°) 的圓周上進(jìn)行輪廓測量
在下圖所示,顯示了 3 個(gè)晶片的粗糙度結(jié)果,每個(gè)晶片的尺寸為 300 mm。它們都用相同的砂輪(粒度#4000)磨削,但使用不同的磨床。在 25 秒內(nèi)用 0.9 毫米的光斑總共進(jìn)行了 40,000 次測量。除了平均粗糙度值的差異外,它還特別表明機(jī)器確實(shí)留下了自己的特征模式。詳細(xì)分析磨削參數(shù)(如進(jìn)給率、卡盤幾何形狀、旋轉(zhuǎn)速度等)的解釋可能會(huì)很有趣。

使用相同砂輪(#4000)
但不同的磨床測量 300 mm 晶片的粗糙度
在下圖中可以看到同時(shí)測量 200 mm背面研磨晶片的粗糙度、形狀(翹曲)和波紋度的示例。雖然砂輪的粒度也是 #4000,但平均 Ra 值要高一些。從磨痕圖案可以看出,旋轉(zhuǎn)是逆時(shí)針方向,從左到右改變方向。翹曲相當(dāng)高,因?yàn)闆]有使用真空。通過應(yīng)用 50 階高通濾波器計(jì)算波紋度。過濾器在圓周上工作,這意味著中心區(qū)域比邊緣和中間區(qū)域過濾得更強(qiáng)烈。將來會(huì)使用不同的過濾方法。波紋結(jié)構(gòu)遵循粗糙模式,但也可見一些從左到右疊加的弱線狀條紋。
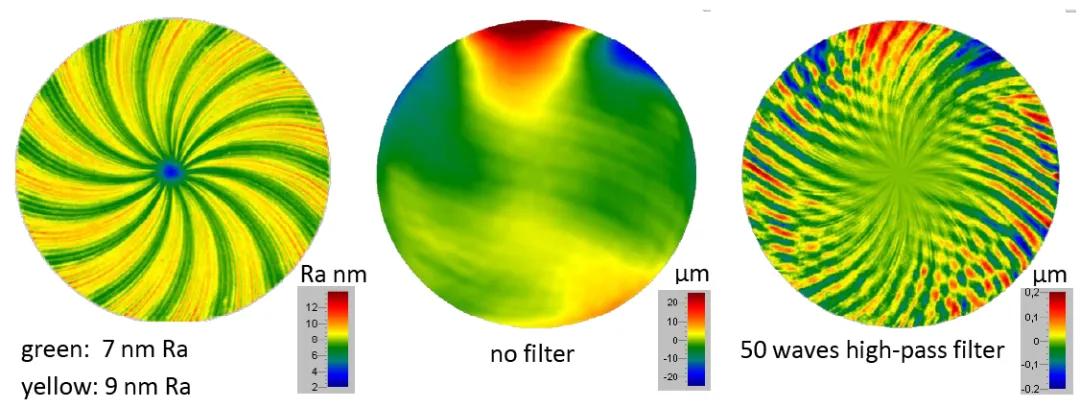
背面研磨 200 mm晶元。
左:粗糙度 Ra,中:翹曲,右:波紋度
? ?這些條紋在下面的測量中更為突出,這是另一個(gè) 200 mm晶片但用 #2000 砂輪研磨的結(jié)果。有趣的不是由較粗的砂輪引起的更高的粗糙度,而是這里的條紋比磨痕的波紋圖案更突出。從 A 到 B 評(píng)估的峰谷高度超過 1 μm,大約是磨痕波紋輪廓高度的 10 倍。
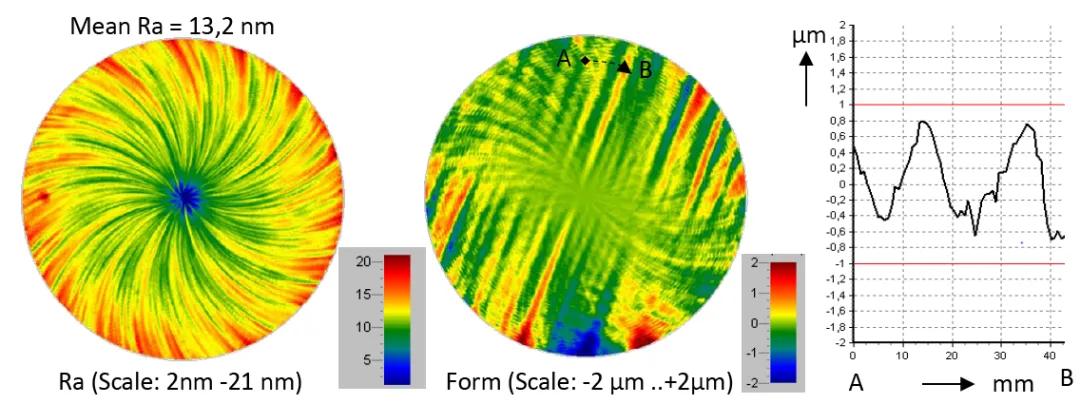
使用 #2000 粒度砂輪研磨的晶片
粗糙度 Ra(左)和波紋度圖(右)
? ?線狀條紋可能是由之前的線鋸過程造成的,在研磨過程后并沒有消失。這可能會(huì)發(fā)生,因?yàn)樵谘心ミ^程中晶片通過真空固定在卡盤上,這使得表面暫時(shí)平坦。當(dāng)晶片在研磨過程后被釋放時(shí),波紋結(jié)構(gòu)恢復(fù)。此外,如果卡盤沒有很好地清潔,同樣的特性會(huì)產(chǎn)生凸起和凹坑。凹痕的示例如下圖所示。300 mm拋光晶片的波紋度圖覆蓋有 2 個(gè)較大的凹痕和一些較小的凹痕。通過使用 0.03 毫米傳感器,可以用更高的局部分辨率再次測量較大的凹坑,并在 3D 地圖中表示出來。寬度在 mm 范圍內(nèi),而深度不超過 1 μm。
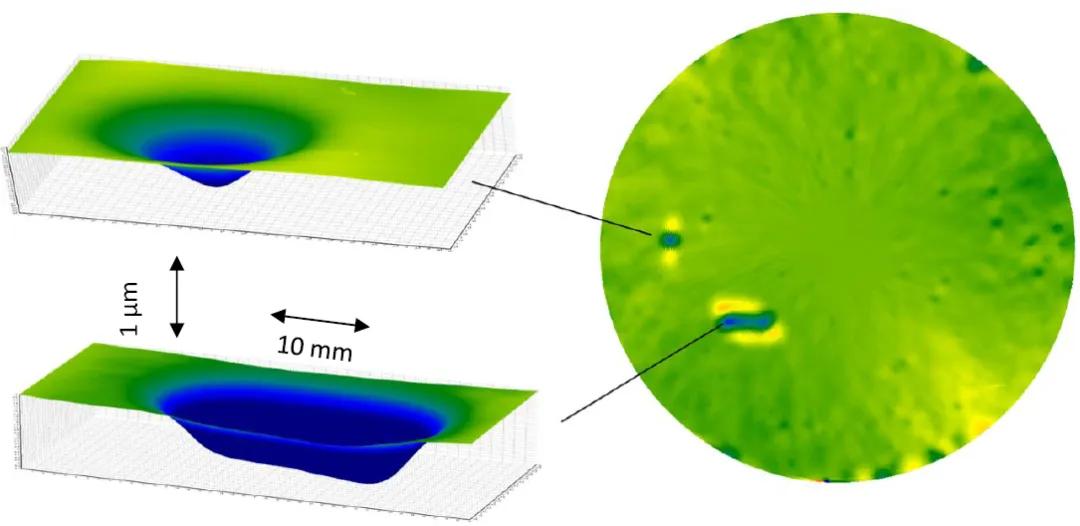
300 mm拋光晶元,帶有凹痕(右 )
具有 0.03 mm 測量點(diǎn)的 3D 表示的高分辨率測量(左 )
高分辨率測量的另一個(gè)例子可以在下圖中看到。這些測量是使用覆蓋 40 mm x 20 mm區(qū)域的 x/y 掃描模塊完成的,也使用 0.03 毫米的小光斑尺寸。測量值代表波紋結(jié)構(gòu)(應(yīng)用 25 階高通濾波器后)。平均粗糙度為 5 nm Ra。在該部分的中心附近可以看到另一個(gè)凹痕。選定的輪廓 (a) 顯示了峰谷高度約為 30 nm 的一般波紋度。重復(fù)性測量表明可以解析 1 nm 高度的結(jié)構(gòu)。

以高橫向分辨率(0.03 毫米光斑)測量的精細(xì)研磨硅晶片表面
左:20 mm x 40 mm區(qū)域波紋度測量和輪廓。
右:相同的區(qū)域,但在凹痕上選擇輪廓。
這使得 WaferMaster 更有趣地用于評(píng)估納米形貌結(jié)構(gòu),以測量 CMP 工藝后的平面化質(zhì)量。此外,從 3D 圖形中可以看出,小點(diǎn)能夠檢測到單個(gè)缺陷(右側(cè)的紅色峰值),并且必須調(diào)查最低缺陷的極限是多少。當(dāng)然,它無法與更強(qiáng)大的散射光系統(tǒng)相抗衡,特別是為前端行業(yè)的小缺陷檢測而設(shè)計(jì),但在后端流程中使用此功能就足夠了。
?
結(jié)論
本應(yīng)用案例中,提出了一種新的散射光傳感器技術(shù)來測量晶片表面,特別是在背面研磨領(lǐng)域。該傳感器通過評(píng)估散射光分布的方差 (Aq) 結(jié)合表面粗糙度測量,并另外使用偏轉(zhuǎn)法來評(píng)估形狀(翹曲)和波紋度。Ra 評(píng)估基于使用共聚焦顯微鏡的相關(guān)性測量??梢宰C明粗糙度測量的靈敏度下降到 Ra = 1 nm,精度為 0.1 nm。這種技術(shù)的優(yōu)勢在于速度(整個(gè) 300 mm晶元掃描為 25 s)和對(duì)環(huán)境機(jī)械噪聲的不敏感性。粗糙度、翹曲和波紋度的全區(qū)域表示功能為表征和改進(jìn)磨削工藝以及從邊緣區(qū)域到中心完全檢查質(zhì)量開辟了新的可能性。
根據(jù)封裝設(shè)計(jì)和背面研磨后工藝的敏感性,邊緣到中心和沿圓周的粗糙度差異以及強(qiáng)烈的翹曲、波紋和缺陷會(huì)影響最終的功能和性能。分離的芯片。模具破損直接取決于粗糙度,特別是磨痕方向。因此,對(duì)背面研磨質(zhì)量的快速和連續(xù)測量有助于提高后端工藝的產(chǎn)量。